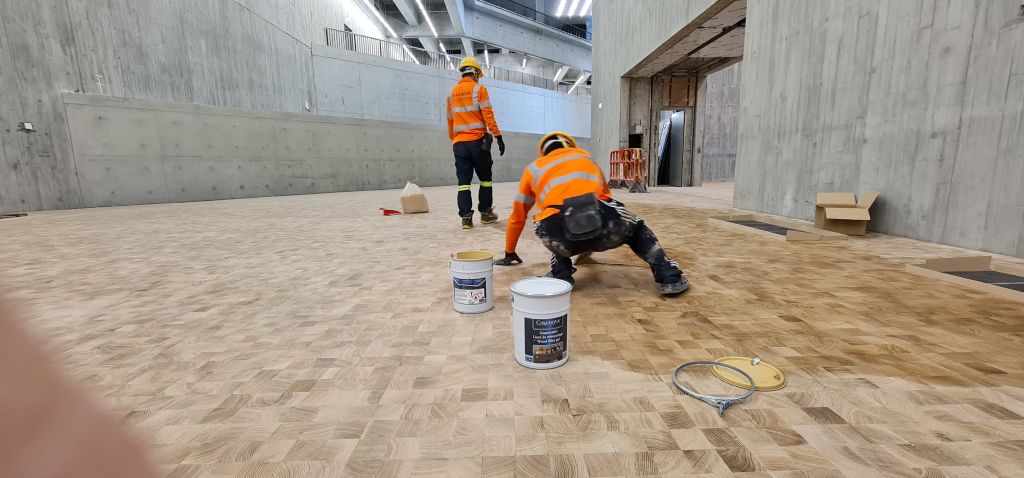
Melbourne parquetry specialist saves the day in Hong Kong's M+ Museum
The grand plan for the flash new museum that will elevate Asia into the big league of international art galleries included a basement exhibition space that would have a floor made of oak cubes.
It would be an artisan component in a concrete volume. It would also be right on trend with the resurgence of traditional skills and materials which architects and interior designers are currently using to enrich resolutely contemporary volumes.
The M+ museum that will open on the foreshore of West Kowloon’s new cultural district in Hong Kong on November 12 is an interesting building by Swiss architects Herzog + De Meuron. It’s shaped like an inverted “T”.
When the LED lights on the edges of the terracotta louvres that band the tower section are lit to display images, the picture is so huge it’s clear from right across Victoria Harbour.
The end-grain oak floor was going to be a gorgeous addition to one of the building’s most important galleries, the B2 level. The trouble was that by leapfrogging traditional techniques and inventing a different way of fabricating and laying it, the architects ended up with an epic fail.
The pre-manufactured product didn’t work. It was splitting before anyone had as much as stepped on it.
Hans Unger, a Melbourne-based parquetry specialist just happened to be in Hong Kong when he received “a random email” asking for his advice on an urgent problem.
He popped around to the still-under-construction M+ building and offered his technical know-how. “I was in the right place at the right time,” he says.
They were impressed with what he imparted about a skill he’s been practising literally at his father’s knee since childhood – “I’ve got pictures of me with a hammer and chisel when I was five” – Unger was duly asked to tender to remediate the floor.
The 47-year-old beat over eight other international firms to get the biggest job he’s ever tackled. He reckons that had a lot to do with the fact that his company, Renaissance Parquet, “already had a hold on the timber”.
The right timber for this exacting application is, he explains, taken from 300-year-old oak trees grown in a specific part of Burgundy, France, “where there is less chalk in the soil, so it’s a harder log without so much sap”.
It’s the timber he imports to use for the more conventional parquetry components he manufacturers in his factory in the Melbourne suburb of Highett. That timber is cut, kiln-dried and turned around in France in about two years.
But the end-grain application demands an even more exacting product, eight years in the drying phase “so that it dries in a natural way and doesn’t crack”. After that time, it spends “another six weeks in the kiln, where it’s heated slowly and cooled slowly”.
The very attractive blocky technique is something Unger has done a few times before for Australian hotels and wine cellars, yet the museum job that was originally to take six weeks but – through a litany of happenstances that included a basement flood and Hong Kong’s notorious humidity – ended up taking eight months.
Within the 33 gallery spaces in the museum of visual culture, which includes art, design, architecture and the moving image, the 1300-square-metre basement is dedicated as the Found Space and will be used for major installations.
It’s going to have heavy machines rolling across the floors during staging, and a lot of punishment from foot traffic during shows. This, Unger says, is where the end grain is ideal, for in the past centuries it was used in industrial and manufacturing settings.
“There was end-grain blockwork between Melbourne’s tram tracks,” he says. “And engineering factories used it. Rough-sanded, they’d tip sump oil over it and buff it in. It’s like a cushion. You can drop a tool on it and the tool won’t break”.
Over the concrete base and by using a technique that he wants to keep a bit obscure but that involves layering and a rubber underpad, then “tensioning and micro-fractioning”, Unger says the now beautiful blonde floor of 300,000 French oak mosaic blocks is ready for the public.
“In the context of the gallery, it’s a perfect fit,” he says. “It looks like it was meant to be there.”
During the intense process that had Unger back on the tools with a team of Nepalese workmen for up to 16 hours a day, he came up with a better description for an old product.
“End-grain: firm, fixed and unchangeable. Like me.”