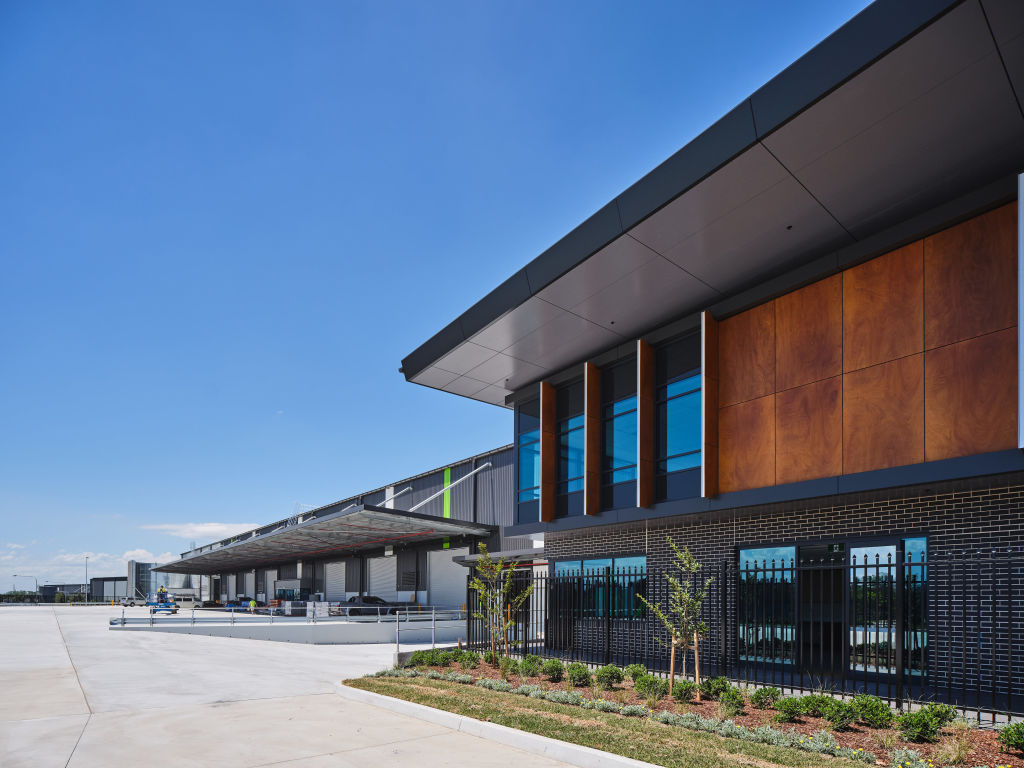
Buyers get in line for prime-grade warehouses as demand rockets
The demand for warehouse space across Australia is at unprecedented levels, especially among businesses that distribute goods, and this is having a huge impact on the market for new industrial buildings with experts seeing more speculative projects and a shift in the types of warehouses being constructed.
“Prime-grade industrial investment stock has never been more sought-after as the market continues to see the flow-on impact from the strength of occupier demand and consequent rental growth,” said Robert Salerno, a partner and head of industrial Australia at Knight Frank.
As a result of that rocketing demand and lack of available supply, it’s estimated that about 1.46 million square metres of industrial property is set to be completed in the eastern seaboard markets by the end of 2019. Of that, 667,000 square metres is in Sydney, 472,000 square metres in Melbourne and 322,000 square metres in Brisbane, according to Knight Frank.
Goodman and Brickworks are developing their Oakdale West estate in western Sydney with an end value of $3 billion, while Amazon opened its second Australian distribution centre in the city’s south-west at Moorebank, nearly twice the size of its Melbourne centre in Dandenong South.
In Adelaide, too, the market is looking strong. Walker Corporation is experiencing robust demand for land at its 200-hectare-plus, $400 million Vicinity Industrial Base in the city’s outer north, which is now about two-thirds of the way through.
“We’re about to release about a dozen lots ranging from 4500 square metres to just short of three hectares,” said Blake Walker. “We’ve had a lot of inquiries from straight warehousing to transport operations, and we’ve had releases brought forward because of the strength of buyer demand.
“We’re seeing a lot of growth in South Australia, with a growing population and a fairly active property market.”
A big chunk of the industrial developments now being built across Australia are speculative projects, making up more than half of the current pipeline, according to Knight Frank. In the past, putting so much money into such an area was considered risky.
“You’re building without a tenant, in the hope of getting one,” said Malcom Tyson, managing director of the industrial division of Colliers International. “But now, vacancies are so tight and so low across many markets, particularly when you go into the different size ranges and grades, it looks a lot less risky.
“The A-grade vacancy rate is unbelievably tight and when a normal lease time-frame goes from three months prior to completion to six months after, when you consider that it’s no different to having an existing building.”
He believes many of the non-speculative facilities being constructed around the eastern seaboard are returning to more specialised kinds of warehouse builds. In the past, warehouses were highly specialised – dependent on whether they were for manufacturing, pick-and-pack or with an office component. Then, with manufacturing moving offshore, they became more generic buildings.
“Now facilities are getting more specialised again because each business has got, for the most part, a slightly different supply base and customer base,” Mr Tyson said. Specialisation emerges as a result of the geography as they want to be in the centre of the most cost-effective location to cut labour and fuel costs.
“The design and level of automation are also important, having to cater to large trucks and a higher volume of small vehicles coming out so the docks and roller doors are important.”
Demand for warehouse space from all tenants is growing annually at 6 per cent, on research by investment bank UBS. But most new builds are now all about the distribution of goods, says Tony Crabb, national director of research at Cushman & Wakefield.
That’s partly the result of population growth, and the increasing demand for consumer goods. But it’s also to cater for the volume of people now buying online.
“So it’s no longer about the distribution of goods to shops but direct to the consumer, to their place of residence, or work,” he said. “Its growth is strong and is moving into regular everyday shopping.
“That requires centres with sophisticated distribution systems to cater to delivering to stores, online same-day delivery, online delivery for three to four days and delivery in two weeks. So the warehouses being built now have new-generation distribution systems required as well. There’s a fascinating evolution in supply chain management using technology to make it faster and cheaper.”
The big issue, however, is the looming shortage of industrial land, particularly in Sydney and Melbourne, Mr Crabb believes, with shortages in central areas of Brisbane also starting to be felt.
That’s further fuelling the trend of building warehouses to greater heights, with automation systems, to make the most of existing land, says Tony Iuliano, head of capital markets industrial & logistics at JLL Australia.
“There’s unprecedented demand for new developments,” he said. “The development pipeline is two-fold – speculative-driven because of that demand and the pre-lease market has never been so strong, and design-to-build from the eastern seaboard, particularly Melbourne. It’s all e-commerce-driven and high-bay automation.
“The food sector is powering along in Australia, and also the pharma sector is driving a lot of the take-up and pre-commitment.”